- Innovation créatrice de nouvelles compétences
- Non
- Innovation génératrice de nouvelles activités
- Oui
- Phase de développement de l'innovation
- Commercialisé depuis plusieurs années
- Date de création
- Date de mise à jour
En bref
La voiture était à peine née qu'il fallait déjà la pourvoir de dispositifs de sécurité. Après le freinage, la tenue de route et l'amélioration de la vision, les développements furent axés sur la protection des occupants en cas d'accident, communément appelée sécurité passive. La zone déformable absorbant l'énergie en cas d'impact frontal a été développée afin de mieux étaler le choc dans le temps et éviter ainsi un niveau de décélération inacceptable pour le corps humain.
Dévoilée sous la forme du concept-car Elixir au salon de Francfort en 2003, la Peugeot 407 fut la première à intégrer une nouvelle voie de transmission d'effort dite voie basse, qui permettait de répartir les forces sur une large surface et de les dévier autour de la cellule des passagers.
La triple voie d'effort reprend cette technologie en tenant compte de la directive européenne sur la réduction des blessures causées aux piétons (octobre 2005) et en facilitant la réparabilité en cas d'accident, ce qui a évidemment une incidence directe sur les coûts d'assurance de la voiture pour son utilisateur.
Et depuis 2009, la « protection piéton » est devenue un critère de notation pour l'Euro NCAP. L'organisme indépendant chargé de tester la sécurité de toutes les voitures en Europe n'attribue plus qu'une seule note globale par véhicule testé intégrant dorénavant un domaine consacré à la protection des piétons. Cependant, le développement semble freiné par l'arrivée des systèmes ADAS visant à éviter les accidents plutôt que de protéger les piétons en cas d'accident.
- Innovation créatrice de nouvelles compétences
- Non
- Innovation génératrice de nouvelles activités
- Oui
- Phase de développement de l'innovation
- Commercialisé depuis plusieurs années
- Date de création
- Date de mise à jour

Description détaillée
La structure d'un véhicule est étudiée pour dissiper l'énergie d'un choc de façon programmée en intégrant un certain nombre d'évolutions comme la triple voie d'effort, pour atteindre des objectifs de sécurité plus
- Protéger au maximum l'habitacle et ses occupants (cellule de survie) ;
- Limiter les lésions occasionnées au piéton lors d'un choc (absorbeurs en plastique) ;
- Faciliter la réparabilité en cas d'accident (réduction des coûts).
En matière de sécurité passive, un véhicule qui bénéficie d'une triple voie d'effort répartit l'énergie en cas de choc frontal, ce qui préserve mieux l'habitacle.
Cette triple voie est constituée :
- D'une voie basse par l'adoption de deux prolonges sur le berceau,
- D'une voie principale ou médiane avec les longerons,
- D'une voie haute, située en partie supérieure des ailes, avec des renforts qui vont guider l'énergie du choc vers les montants de baies et les profilés de portes.
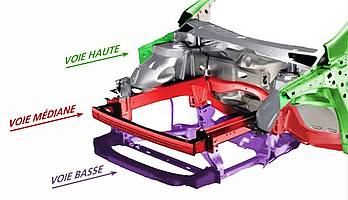
La répartition d'énergie, dans ce cas, se fera à 60 % par la voie médiane, à 20 % par la voie basse, et les 20 % restant par la voie haute.
En répartissant mieux l'énergie, ce type de structure permet une synthèse intéressante entre la souplesse, pour protéger les piétons et limiter les dégâts lors de chocs légers, mais aussi la rigidité, pour la protection des passagers contre les chocs frontaux à vitesse élevée en canalisant la déformation de la coque loin de la partie inférieure des jambes des passagers avant.
La voie médiane, depuis toujours la principale voie d'absorption d'énergie, est une association d'aciers spécifiques (ADX, HLE, THLE et UHLE). La protection des piétons est confiée à un absorbeur souple intégré au bandeau de pare-chocs ou fixé sur la poutre de pare-chocs, qui est généralement en acier ou en aluminium extrudé.
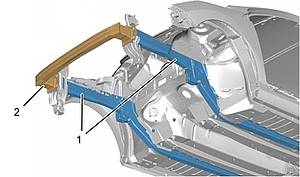
(Source PSA)
(1) Longerons (en acier HLE, épaisseur 2,44 mm)
(2) Traverse supérieure de façade avant (en alliage d'aluminium)
Sur certains véhicules, on utilise des absorbeurs d'énergie compacts pour limiter le porte-à-faux avant et faciliter la réparation, le système d'absorbeurs « Bogé Wagon » (nom du détenteur du brevet) situé dans la poutre de pare-chocs avant.

(Source PSA)
(1) Longeron avant
(2) Absorbeur conique en acier
(3) Poutre en acier
La poutre s'appuie sur deux absorbeurs coniques à déformation programmée. L'absorption d'énergie (85 kN) permet de limiter l'impact sur les brancards et d'éviter ainsi leur remplacement lors des chocs inférieurs à 15 km/h.
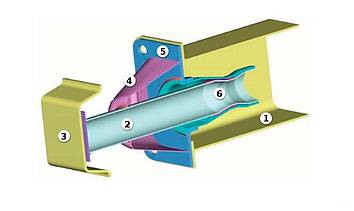
(1) Longeron avant
(2) Tube à déformation
(3) Poutre de pare-chocs en acier
(4) Cône de stabilité à déformation programmée
(5) Absorbeur conique en acier
(6) Zone de déformation programmée
Le système se déforme en deux temps :
- Le tube central s'enfonce dans le petit cône et crée une première force de retenue.
- Un niveau supérieur d'absorption programmée est ensuite généré par l'écrasement du plus grand cône.
La voie basse est constituée d'un berceau plus long, obtenu avec un berceau standard, auquel ont été ajoutés deux prolonges, une traverse avant, des botteleurs et une poutre piéton équipée d'absorbeurs. Cette poutre en matière composite avec absorbeurs intégrés qui est positionnée comme élément final de la voie basse et sert à repousser la jambe pour éviter les graves traumatismes du genou.
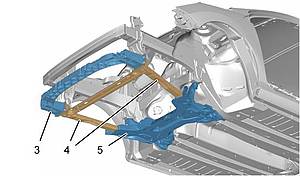
(Source PSA)
(3) Traverse façade avant inférieure (en thermoplastique, avec d'excellentes propriétés d'absorption d'énergie et très légère)
(4) Allonges de berceau (en alliage d'aluminium)
(5) Berceau avant
La voie haute, troisième zone de dissipation d'énergie va décrire une stratégie d'absorption déterminant l'empilage des efforts pour les transmettre, par des « chemins » préétablis, vers des zones conçues pour résister aux chocs ; le tablier, le soubassement, les côtés de caisse, ou encore les raidisseurs de portes avant entretoisant les pieds avant et milieu.
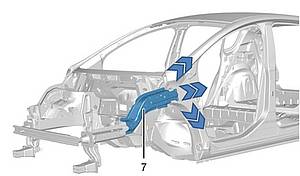
(Source PSA)
(7) Renfort de côté d'habitacle (en acier HLE)
D'autre part, sur cette voie haute et toujours par souci de préserver au maximum l'intégrité des piétons, la souplesse structurelle de la face avant et dans le même esprit, les pattes de fixation « fusibles » des projecteurs qui autorisent leur descente sous le capot en cas de choc, complètent avantageusement le dispositif.
On notera aussi que sur certains véhicules, le dessous du capot a été étudié afin d'assurer un espace important entre le capot et les éléments mécaniques. Cette « zone de survie » permet d'amortir le corps qui peut s'enfoncer sur une course importante sans heurter de point dur. Le plus souvent, les modèles qui ne peuvent pas garantir cette distance d'enfoncement sont équipés d'un système de relevage du capot.
De plus, la voie haute et la voie basse sont en principe entretoisées, ce qui permet d'optimiser la rigidité et la stabilité de l'ensemble. Cette structure avant ainsi constituée concrétise une stratégie d'absorption des chocs évoluée. Elle permet de mieux répartir l'énergie et donc de présenter une intéressante synthèse :
- La voiture est nécessairement rigide pour la protection contre les chocs frontaux de type haute vitesse. À noter que le recul limité du groupe motopropulseur par un impacteur (dispositif d'accrochage du groupe motopropulseur sur le berceau) et la colonne de direction rétractable complètent souvent le dispositif de protection.
- Mais elle est suffisamment souple, localement, pour assurer la protection des piétons ainsi que la compatibilité lors de chocs avec des véhicules plus légers.
On retrouve un principe identique sur les structures en aluminium.
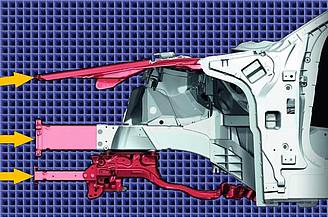
Diffusion sur le marché | Tous les constructeurs intègrent désormais des technologies pour diminuer la gravité des accidents lors d'une collision entre un véhicule et un piéton.
|
---|---|
Constructeurs concernés | Ce dispositif en particulier est principalement utilisé par PSA et Audi pour les structures en aluminium. |
Innovation engendrant des entretiens | Non |
Innovation engendrant des réparations | Non |
Dispositif législatif en rapport avec l'innovation | Mise en œuvre dès 2005, la directive 2005/66/CE « choc piéton » élaborée par la Commission Européenne. En 2011, création de la norme ISO 11096 établissant une méthode d'essai pour évaluer la protection d' |
Contrôle technique | La technologie présentée ici est soigneusement examinée lors des contrôles techniques Les anomalies recherchées et évaluées sont :
|
Mots-clés | Troisième voie d'effort, triple voie d'effort |
Méthodes et pratiques
Le système de répartition des voies d'effort ne nécessite pas d'entretien ou de réparation sans qu'il ne soit endommagée par un accident de la route. Il peut dans ce cas être réparé.
Un diagnostic de la réparation va permettre de déterminer l'étendue et la profondeur des dégâts et de définir les moyens et les méthodes nécessaires à la réparation du véhicule.
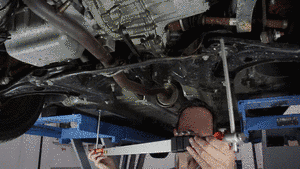
Une remise en forme légère est possible, à partir du moment où le profil initial peut être parfaitement retrouvé, sans rechargement de matière.
Il faut néanmoins se souvenir que le chauffage d'une tôle à haute limite élastique pour faciliter la remise en forme est à proscrire.
Des dommages légers sur les éléments en matière plastique peuvent être réparés par collage ou soudage, mais le coût modéré des pièces limitera ce type d'intervention.
Les critères de conformité (définis par le constructeur), sont l'esthétisme, le fonctionnement et la sécurité. Si l'on ne peut pas satisfaire à ces critères, il faut songer à remplacer l'élément.
Il faut se référer aux préconisations du constructeur quant à la méthode de remplacement à mettre en œuvre qui peut être vissée ou soudée.
Vissé pour la voie basse et la traverse de la voie médiane
Déposer le pare-chocs avant.
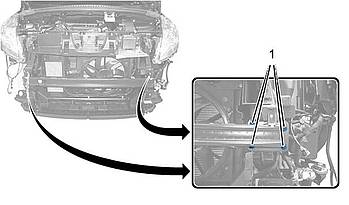
(Source PSA)
Déposer les vis (1).
Procéder de la même manière pour l'autre côté.
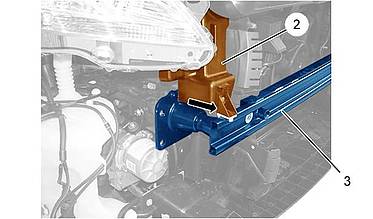
(Source PSA)
Écarter la garniture (2) avec précaution.
Déposer la poutre centrale avant (3) suivant la flèche.
Pour la repose procéder dans l'ordre inverse des opérations de dépose.
Serrer les vis (1) à 2 m.daN.
Reposer le pare-chocs avant et vérifier le fonctionnement des équipements.
Soudé pour les longerons (en voie médiane) et les renforts de la voie haute
Dans ce cas il faudra effectuer :
- Soit un remplacement partiel ;
- Soit un échange complet de l'élément.
Il est impératif de respecter les consignes de sécurité et de propreté.
Toutes les surfaces décapées doivent être protégées par le procédé de rezingage électrolytique homologué.
Pour ces opérations un banc de mesure est obligatoire.
Des opérations complémentaires seront nécessaires :
- Débrancher la batterie.
- Déposer ou protéger les pièces qui se trouvent dans la zone de réparation et qui peuvent être détériorées par la chaleur ou la poussière.
- Dégager les faisceaux électriques.
Entreprises concernées aujourd'hui | Carrosserie / Peinture, MRA, RA2, RA1 |
---|---|
Métiers concernés | Carrossier et Peintre, Réceptionnaire |
Impact sur les compétences en atelier
-
Exemple d’outillage approprié
Pige de mesure télescopique 415÷925 mm avec accessoires pour mesure comparative.
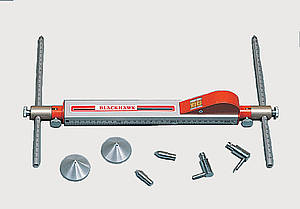
À lire aussi dans la même section

La recherche de teinte avec un Smartphone
Les logiciels de recherche couleur présents sur tous les outils informatisés de pesée des marques de peinture sont accessibles depuis un Smartphone ou une tablette. La recherche de teinte est ainsi à...

Le vernis rapide à séchage AIR
De nombreux fabricants proposent une gamme de vernis nouvelle génération pouvant sécher à l'air libre (autrement dit : sans étuvage cabine ni séchage par infrarouge), permettant ainsi de réduire les...

Les biomatériaux
Les biomatériaux, tels que les biopolymères, ne sont pas des produits récents. Au milieu du vingtième siècle, Henry Ford a inventé une méthode de fabrication de pièces d'automobile en plastique à...

L'application par transfert hydrographique
L'impression hydrographique est aussi appelée impression par transfert par eau (Water Transfer ou Hydro Dipping en anglais).
Cette technique d'application permet de transférer un film aux motifs pré...