- Innovation créatrice de nouvelles compétences
- Oui
- Innovation génératrice de nouvelles activités
- Oui
- Phase de développement de l'innovation
- Commercialisé depuis plusieurs années
- Date de création
- Date de mise à jour
En bref
Il est trop tôt pour dire si la structure mixte deviendra le courant dominant de la construction automobile. Les deux constructeurs, Audi et BMW, semblent convaincues que les caractéristiques de chaque matériau peuvent être combinées pour fabriquer un véhicule solide et durable.
L'objectif imposé aux constructeurs pour 2020 est de réduire de manière importante les émissions de CO2, ce qui se traduira par une réduction de la masse de leur carrosserie d'environ 160 kg.
Dans ce contexte, l'augmentation de la quantité d'acier à haute résistance est très significative, l'aluminium regagne du terrain et le potentiel d'évolution des matériaux composites est considérable, on estime que d'ici 2 ans, ⅓ des matériaux utilisés dans la fabrication des véhicules seront des composites.
En privilégiant l'un ou l'autre matériau de fabrication, on pourrait gagner dans l'absolu :
- 50 kg avec un véhicule tout acier à très haute résistance,
- 150 kg avec des alliages d'aluminium,
- 200 kg avec exclusivement des composites.
Mais, bien sûr, ce ne sera pas le cas pour des raisons liées au coût et pour des contraintes diverses.
Tout laisse à penser que la voiture de demain sera multi matériaux.
- Innovation créatrice de nouvelles compétences
- Oui
- Innovation génératrice de nouvelles activités
- Oui
- Phase de développement de l'innovation
- Commercialisé depuis plusieurs années
- Date de création
- Date de mise à jour

Description détaillée
C'est une structure fabriquée en utilisant deux matériaux différents, principalement l'acier et l'aluminium.
Les concepteurs automobiles ont continuellement cherché à trouver des solutions visant à réduire le poids d'un véhicule, tout en maintenant la résistance à l'écrasement et ses caractéristiques.
Cette structure permet d'équilibrer les charges sur essieux afin d'améliorer le comportement de la voiture, valorisant ainsi les qualités dynamiques du véhicule.
Au cours des dernières années, tous les constructeurs automobiles ont dû faire face au problème grandissant du poids des véhicules. Les moteurs devenant de plus en plus puissants, le châssis et la carrosserie doivent supporter et transmettre des forces toujours plus élevées.
De plus, l'habitacle et le véhicule dans son ensemble deviennent toujours plus grands et ce, du fait que la taille du véhicule est déterminée en prenant comme base de référence la taille moyenne de la population.
Il ne faut pas oublier non plus le fait que les exigences de sécurité et de confort n'ont cessé de croître ces dernières décennies, en conséquence de quoi un nombre toujours plus grand de systèmes de sécurité et de confort sont proposés de série ou en option. Ces différentes évolutions ont eu pour conséquence d'alourdir les véhicules et en cinquante ans, le poids moyen des véhicules a augmenté de 60 %.
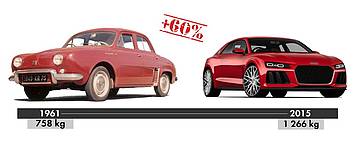
Les concepteurs automobiles se sont fixés comme objectif d'enrayer voire d'inverser cette tendance.
Avec le durcissement des normes en matière d'émission de CO2, les constructeurs automobiles sont amenés à revoir les stratégies. En effet, un véhicule allégé de 110 kg émet en moyenne 10 g de CO2 /km en moins.
Depuis de nombreuses années déjà, certaines pièces métalliques de nos véhicules ont fait place à leurs homologues en matériaux moins denses. Ainsi, polymères et composites ont progressivement remplacé l'acier pour des pièces de carrosserie (pare-chocs, ailes, hayons, bacs de roue de secours) ou de nombreux éléments de l'habitacle. Dans les moteurs, la fonte des culasses fait progressivement place à l'aluminium, beaucoup plus léger. Pour le châssis ou la structure, les alliages d'aciers à haute résistance ou l'utilisation d'alliages d'aluminium ont permis la réalisation d'éléments à la fois plus légers et capables de mieux absorber l'énergie d'un choc.
Deux constructeurs font figure de précurseurs dans ce domaine.
Tout d'abord BMW, avec la série 5 E60 qui était le premier véhicule à disposer d'une structure mixte de type aluminium/acier. Le bloc avant est en aluminium et l'habitacle ainsi que le bloc arrière sont en acier, on verra cette technologie aussi sur les Série 6.
Il a été possible, grâce à cette structure mixte et à l'utilisation d'aciers à haute résistance, d'alléger la carrosserie de 255 kg (ouvrants non compris) et d'améliorer sensiblement la répartition des masses.
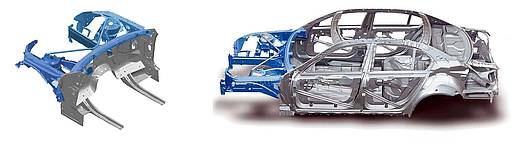
En bleu, les parties en aluminium et en gris les aciers
Suivi quelques temps plus tard, par Audi et son Coupé TT constitué non seulement des pièces moulées en aluminium, des profilés extrudés en aluminium et des tôles d'aluminium, savoir-faire maîtrisé par ce pionnier de la technologie de l'allègement, mais aussi des éléments en tôle d'acier. La mise en œuvre de tôles d'acier dans la partie arrière de la carrosserie a permis d'optimiser la répartition du poids du véhicule. Cela exerce une influence directe sur les caractéristiques sportives, telles que dynamique de roulage et accélération, ainsi que sur les caractéristiques de sécurité, telles que distance de freinage et stabilité directionnelle. En dépit de la mise en œuvre partielle d'éléments en tôle d'acier, le poids total de la carrosserie, soit 277 kg avec les pièces rapportées comme les portes et les capots, est nettement inférieur à celui d'une carrosserie acier intégrale comparable (350 à 400 kg) tout en ayant une résistance plus élevée et une rigidité en torsion 50 % supérieure.
La TT Coupé est constituée de près de 70% d'aluminium (en bleu), les 30% restants étant en acier (en rouge).
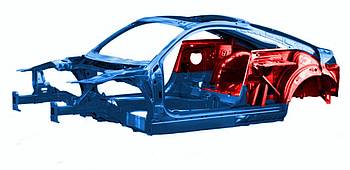
A cette époque et bien que les véhicules à structure mixte soient encore peu répandus, Audi et BMW ont prouvé que ces matériaux peuvent être utilisés ensemble, à condition que des mesures préventives contre la corrosion soient prises.
En raison de l'utilisation de deux métaux différents, il existe des préoccupations sur la corrosion galvanique. Au cours des processus de fabrication du véhicule, tous les liens entre l'aluminium et l'acier sont isolés avec un adhésif structurel non conducteur. En plus de l'adhésif, d'autres modes de fixation sont utilisés, comme le rivetage auto-poinçonneur ou le vissage Flowdrill.
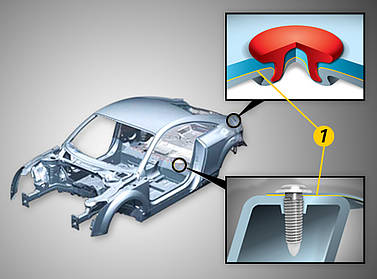
(1) colle
Des procédés d'assemblage thermique tels que le soudage MIG étant exclus car ne permettant pas de réaliser une liaison possédant une résistance statique et dynamique suffisante, sans risques de corrosion par contact.
Les liaisons aluminium-acier peuvent, en cas de protection anticorrosion déficiente, présenter des taux de corrosion beaucoup plus élevés que des liaisons aluminium-aluminium ou acier-acier. Le respect d'exigences qualitatives maximales doit par conséquent être assuré sur chaque carrosserie lors de la réalisation de cette liaison, en production comme en après-vente.
La base de la protection anticorrosion des liaisons aluminium/acier galvanisé sujettes à la corrosion est constituée par un collage au niveau de la caisse en blanc. Cela permet d'obtenir une isolation de grande surface des « partenaires », réduisant les processus de corrosion au niveau du point de contact. Une autre mesure consiste à étancher tous les assemblages mixtes avec du PVC après la cataphorèse au trempé ou de les protéger avec de la cire.
Le problème de la corrosion résolu, les deux constructeurs allemands appliquent ces nouveaux principes à d'autres véhicules.
Avec le concept allégé, Audi fait appel à la fonte d'aluminium pour les jambes de force de la A7 qui seront assemblées par collage/rivetage sur le reste de la structure en acier.
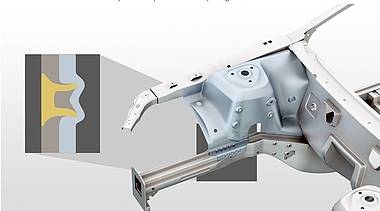
Ou inversement, pour la carrosserie de la A8, tout en pérennisant le concept Aluminium Space Frame qui a fait ses preuves, introduire un montant B (pied de milieu) en acier THLE trempé directement après formage à chaud. Cette construction permet d'optimiser encore la rigidité de la carrosserie ainsi que son comportement en collision. Ici l'assemblage est réalisé par vissage Fowdrill en partie haute.
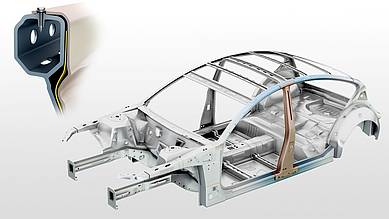
BMW va encore plus loin, pour ces véhicules tout électrique i3 et i8, le constructeur conçoit des structures mixtes fabriquées autour d'un habitacle en matière plastique renforcé de fibre de carbone (jusqu'à présent difficilement applicable à des productions de série) et complété de deux structures, avant et arrière, en aluminium ou d'un châssis de technologie Space frame également en aluminium. Ces matériaux composites à faible densité sont utilisés parce qu'ils garantissent une stabilité supérieure à celle de l'aluminium et une réduction de poids de 50 % par rapport à l'acier. Dans le même temps, la Série 7 intègre à sa structure métallique des éléments en fibre de carbone, comme la traverse supérieure de pare-brise notamment.
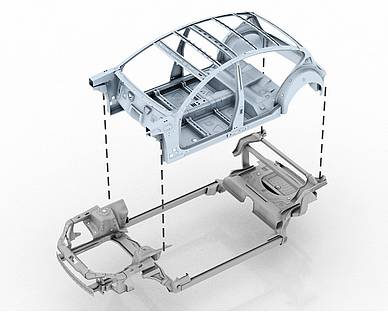
Le chassé-croisé pour le leadership est lancé, Audi fait évolué sa TT avec des aciers à haute limite élastique pour la partie inférieure et l'aluminium pour la partie supérieure. Comme sa cousine la Lamborghini Huracan, la dernière R8 combine l'aluminium et un polymère renforcé de fibres de carbone (PRFC). Après le concept Sport Quattro, la A4 a encore repoussé les limites de la construction mixte en alliant les trois matériaux. Une combinaison inédite d'acier pour la partie inférieure de la structure, d'aluminium pour la partie supérieure et de PRFC pour le pavillon.
La dernière génération de son vaisseau-amiral, la A8, dispose d'une structure composée à 58% d'aluminium, des alliages d'acier à haute résistance ainsi que de l'acier conventionnel selon les sections, d'une barre de renfort en magnésium à l'avant et d'un panneau arrière séparant l'habitacle du coffre en PRFC.
Diffusion sur le marché | L'utilisation de structure mixte reste réservée à quelques modèles prémium.
|
---|---|
Constructeurs concernés | BMW, Audi, Lamborghini, Porsche et Alfa Roméo |
Innovation engendrant des entretiens | Non |
Innovation engendrant des réparations | Non |
Dispositif législatif en rapport avec l'innovation | La responsabilité du carrossier en réparation automobile est de respecter les règles de l'art telles que définies par la Norme Française NF X 50-210 de 1992 et de tenir compte des évolutions technologiques. Instruction technique d |
Contrôle technique | La différence avec le monocoque en aluminium vient du fait que dans le premier cas, toute la coque est réalisée en aluminium et que des éléments de carrosserie acier peuvent être ajoutés, alors qu'ici, c'est la structure même du véhicule qui est composée de deux métaux différents, avec les risques que cela peut comporter, surtout après une réparation non maîtrisée. |
Mots-clés | Structure, hybride, acier, aluminium |
Méthodes et pratiques
La structure mixte, comme son homologue tout en aluminium, ne nécessite pas d'entretien ou de réparation sans qu'elle soit endommagée lors d'un accident de la route. Elle peut dans ce cas être réparé.
Dans le cas d'une collision, un endommagement d'éléments de carrosserie en aluminium comme en acier est possible. L'endommagement d'une pièce du bloc arrière en acier (1) et du panneau latéral aluminium (2) par exemple sur l'Audi TT.
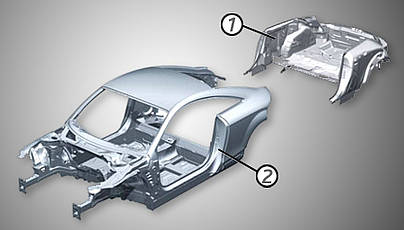
Après dépose des éléments endommagés, les pièces neuves sont montées conformément aux procédures de réparation de chaque constructeur.
Les travaux sur les assemblages d'éléments de carrosserie acier et aluminium requièrent un soin particulier pour éviter tout risque de corrosion par contact ultérieure.
Dans les zones d'assemblage, utiliser une colle pour carrosserie bi-composants et des rivets ou des vis. La colle permet d'obtenir une couche isolante entre les deux matériaux, et ainsi d'éviter la corrosion par contact.
Pour une réparation ne concernant que des éléments en acier, sans endommagement de l'assemblage acier/aluminium, la démarche est identique à celle applicable dans le cas d'un véhicule tout acier.
Il est toutefois important de prendre des mesures de précaution particulières :
- Procéder exclusivement aux découpes par enlèvement de copeaux avec une scie alternative et non par meulage.
- Si un ponçage est indispensable, travailler avec des disques de ponçage ne provoquant pas ou peu de projection d'étincelles.
- La poussière de ponçage des éléments en acier, tout comme les étincelles projetées lors d'opérations de découpe ou de soudage ne doivent pas entrer en contact avec les pièces aluminium.
- Les mêmes mesures sont applicables aux pièces d'aluminium peintes. Des particules d'acier incandescentes peuvent provoquer l'endommagement de la peinture et une particule d'acier pouvant entrer ainsi en contact avec l'élément en aluminium, risquant d'être à l'origine d'une corrosion par contact.
- Pour les opérations de soudage, utiliser dans la mesure du possible la machine de soudage par points, qui cause moins de projections.
- Dans le cas d'un soudage sous atmosphère protectrice, ne fixez en aucun cas la pince de masse sur les éléments en aluminium.
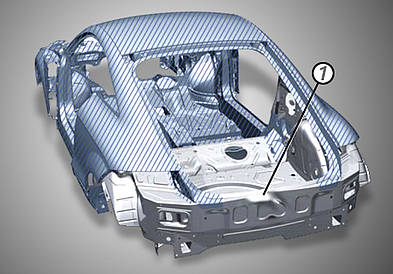
Lorsque l'on réalise une réparation sur des éléments en acier (1), il faut protéger méticuleusement l'intégralité de la carrosserie avec des couvertures anti-feu.
Les différents éléments en aluminium étant assemblés au moyen de rivets auto-poinçonneurs, la conductivité électrique a tendance à diminuer avec le temps et à devenir moins bonne qu'avec des liaisons soudées conventionnelles.
Lors d'une réparation, il est important de rétablir la conductivité électromagnétique à l'aide de vis CEM M5 auto taraudeuses en acier à revêtement spécial. En cas de non-respect de cette consigne, tous les composants situés en aval du point de sectionnement ne sont plus correctement reliés à la masse. En présence de champs magnétiques haute fréquence (par exemple le système d'allumage), ces composants agissent comme des antennes émettrices. Les ondes électromagnétiques peuvent perturber à la fois la réception de la radio et les boîtiers électroniques embarqués. Un courant élevé risque par ailleurs de circuler dans les rivets, ce qui peut provoquer l'échauffement de ceux-ci et par là-même l'endommagement de la colle.
Entreprises concernées aujourd'hui | Carrosserie / Peinture, MRA, RA2, RA1 |
---|---|
Métiers concernés | Carrossier et Peintre, Réceptionnaire |
Impact sur les compétences en atelier
- Connaître les méthodes de diagnostic d'un véhicule accidenté
- Connaître les différents matériaux de fabrication de carrosserie automobile (caractéristiques, composition, localisation…)
- Connaître les méthodes d'assemblage d'une structure mixte
- Connaître les méthodes de redressage de l'acier et de l'aluminium
- Savoir réaliser un diagnostic d'un véhicule accidenté
- Savoir souder l'acier (soudure MAG et SERP)
- Savoir souder l'aluminium (soudure MIG)
- Savoir utiliser les différents outillages préconisés (riveteuse, …)
- Savoir utiliser les produits de collage
- Savoir remettre en forme un élément en acier et en aluminium
- Savoir refaire les traitements de surface acier et aluminium
Exemple d’outillage approprié
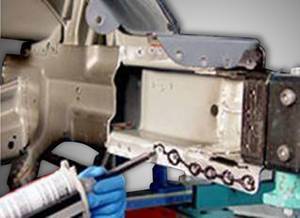
Pistolet à colle bi-composant
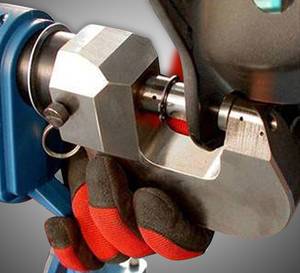
Pince à rivet auto-poinçonneur
À lire aussi dans la même section

Les biomatériaux
Les biomatériaux, tels que les biopolymères, ne sont pas des produits récents. Au milieu du vingtième siècle, Henry Ford a inventé une méthode de fabrication de pièces d'automobile en plastique à...

Les tôles sandwich
Le matériau sandwich multicouches comme principe de construction n'est pas nouveau (Brevet de juillet 1924).
Des applications de ce procédé se retrouvent non seulement dans la construction...

Le magnésium
Ce métal, le 4ème élément le plus abondant (après le fer, l'oxygène et le silicium) sur terre, est en progression lente mais constante dans l'industrie automobile. Il faut bien noter que la fonderie...

Le Noryl
En 1964, Général Electric commercialise la résine modifiée PPO Noryl et en 1988, avec la résine Noryl GTX, la société américaine offre de multiples avantages pour la conception d'ailes et autres...