- Innovation créatrice de nouvelles compétences
- Oui
- Innovation génératrice de nouvelles activités
- Oui
- Phase de développement de l'innovation
- Commercialisé depuis plusieurs années
- Date de création
- Date de mise à jour
En bref
L'arrivée du Common rail a eu un fort impact sur les clients de véhicules diesel :
- Baisse des consommations
- Nette diminution du bruit de fonctionnement
- Image de véhicule non polluant
Tous ces avantages découlent de la précision de fabrication apportée aux injecteurs. Le système Common rail est complexe de par la technologie de l'injecteur et de sa gestion très performante.
L'injecteur est une pièce qui coûte cher, bon nombre de clients ayant fait les frais de remplacement de modèles défectueux.
La haute technologie induit un niveau de risque en rapport. De fait, la souscription par le client à une extension de garantie se justifie de plus en plus.
Le problème réside dans la réparation de véhicule âgés et/ou très kilométrés. En effet, les coûts de remise en état sont tels qu'ils en réduisent considérablement la valeur vénale et donc pose la question de la destination finale de ce type de véhicules.
- Innovation créatrice de nouvelles compétences
- Oui
- Innovation génératrice de nouvelles activités
- Oui
- Phase de développement de l'innovation
- Commercialisé depuis plusieurs années
- Date de création
- Date de mise à jour

Description détaillée
Avec le durcissement des normes de dépollution, les constructeurs ont dû changer de système d'injection. L'injecteur électromagnétique Bosch est apparu avec les premiers systèmes Common rail en 1998 (HDI, DCI, TDCI…).
Ces injecteurs permettent :
- de pulvériser le gasoil très finement ;
- d'injecter des volumes de gasoil très précis.
L'injecteur électromagnétique est une évolution de l'injecteur classique. C'est-à-dire que le principe de pulvérisation reste identique (aiguille et buse). En revanche, il a été ajouté une partie électrique qui permet de commander l'ouverture de l'aiguille.
Rappel sur le fonctionnement d'un injecteur classique.

Ouverture d'un injecteur classique :
La pompe à injection refoule le gasoil qui vient exercer une pression sur le cône de poussée de l'aiguille (1). Quand la force exercée sur le cône dépasse la force de tarage du ressort, l'aiguille se soulève, il y a donc injection.
Fermeture d'un injecteur classique :
Lorsque la pompe distributrice arrête de refouler, la pression chute, le ressort repousse l'aiguille sur son siège. C'est la fin de l'injection de carburant.
Les normes de dépollution nécessitent :
Une pulvérisation plus fine du gasoil (homogénéisation du mélange et réduction du délai d'inflammation des gouttelettes).
Un découpage de l'injection (pré injection et injection principale) adapté aux conditions de fonctionnement du moteur.
Un accroissement de la précision du débit injecté.
Description de l'injecteur Bosch électromagnétique :

Principe de fonctionnement :
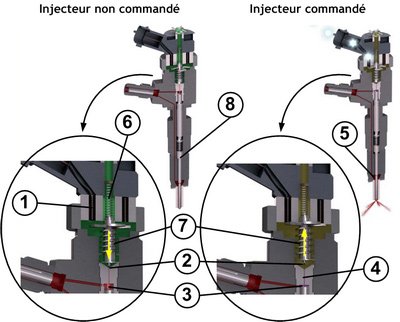
1. Bobine
2. Bille
3. Chambre de commande
4. Ajutage de fuite
5. Chambre de pression
6. Ressort de valve
7. Ancre + piston de commande de la bille
8. Aiguille
Injecteur fermé : L'actionneur n'est pas piloté (bille de commande (2) est fermée). La pression de la chambre de commande (3) est égale à la pression de la chambre de pression (5). La pression sur le piston de commande de l'aiguille (8) et le ressort de l'injecteur maintiennent l'aiguille (8) sur sa portée d'étanchéité.
Ouverture de l'injecteur : Piloté par le calculateur sous une tension de 80 volts, l'actionneur électromagnétique déplace la bille de commande (2). La pression dans la chambre de commande (3) chute par l'ajutage du circuit de retour (4), la force F1 sur le piston de commande de l'aiguille (8) diminue. Le piston de commande et l'aiguille de l'injecteur se soulèvent.

L'ajutage du circuit d'alimentation évite l'équilibrage des pressions. L'aiguille de l'injecteur dégage les orifices d'injection. Le carburant est injecté dans le moteur.
Dans ce cas: F1+Fr < F2 = injecteur ouvert.
F1 = pression dans la chambre de commande
Fr = force du ressort
F2 = pression dans la chambre de pression
Fermeture de l'injecteur : Le calculateur cesse de commander l'actionneur électromagnétique. La bille de commande (2) est repoussée sur son siège par le ressort de valve (6), l'ajutage du circuit de retour (4) se ferme, permettant à la pression dans la chambre de commande (3) de redevenir identique à la pression du rail. L'équilibre des pressions est de nouveau rétabli, la force F1 sur le piston de commande de l'aiguille (8) redevient élevée. L'aiguille de l'injecteur ferme les orifices d'injection.
Dans ce cas: F1+Fr > F2 = injecteur fermé.
Nota: Lorsque les pressions sont identiques dans les chambres de commande (3) et de pression (5), la force F1 est toujours supérieure à la force F2, car la surface d'application de la pression sur le piston de commande de l'aiguille (8) est plus grande que la surface d'application de la pression sur le cône de l'aiguille de l'injecteur (8). Le ressort de l'injecteur sert également à maintenir l'aiguille de l'injecteur fermée (étanchéité de l'injecteur) lorsqu'il n'y a pas de pression dans le rail (moteur arrêté).
Visualisation de l'animation flash d'un injecteur électromagnétique
La buse et l'aiguille de l'injecteur.
L'aiguille d'un injecteur d'un véhicule diesel effectue plus d'un milliard de courses d'ouverture et de fermeture pendant sa "vie d'injection". Elle doit assurer l'étanchéité jusqu'à 2050 bar et subir un certain nombre de contraintes :
L'absorption des chocs d'ouverture et de fermeture rapides (sur une voiture, ils se produisent jusqu'à 10000 fois par minute si le moteur fonctionne avec pré-injection et post-injection).
La résistance aux contraintes d'écoulement élevées lors de l'injection est tenue à la pression et à la température dans la chambre de combustion.
Quelques valeurs propres aux injecteurs :
L'injecteur subit des pressions de l'ordre de 2050 bar, pour assurer l'étanchéité entre l'aiguille et la buse (12) le jeu fonctionnel est de 0,002 mm (Cheveu humain 0,06 mm de diam.). Des volumes de carburant de l'ordre de 50 mm3 sont refoulés via les orifices d'injection (10) (d'une section d'environ 0,110 mm²) en moins de 2 ms à la vitesse de 2000 km/h.
Toute ces contraintes imposent un grand savoir faire dans les domaines du développement, de la science de matériaux, de la fabrication et des méthodes de mesure.
La buse de l'injecteur :
L'amélioration de la fiabilité dans le temps de l'injecteur (très sollicité) passe, entre autre, par une évolution du process de réalisation de la buse. Les orifices réalisés dans la buse grâce au principe de l'électroérosion (dont le diamètre est de l'ordre 110 µm) ont une forme rectiligne. Lors de l'ouverture de l'aiguille de l'injecteur, il se crée un phénomène de cavitation qui perturbe l'écoulement du carburant (modification du débit injecté) et favorise l'arrachement de matière dans la buse.
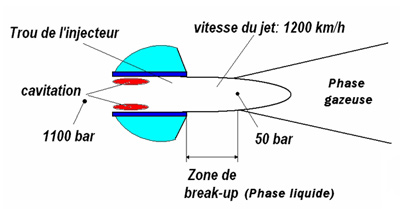
Pour limiter ce comportement néfaste à la longévité de l'injecteur, Bosch réalise des buses du type « KS » dont les trous ont une forme conique :
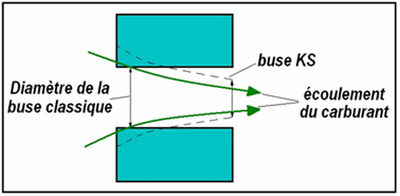
De plus, les impacts répétés entre l'aiguille et la buse (fermeture de l'injecteur) ont pour effet de réduire le diamètre du siège de l'aiguille ce qui provoque :
Une augmentation de la surface d'appui pour la force d'ouverture de l'injecteur.
Une ouverture prématurée de l'injecteur ce qui entraine une augmentation du débit injecté.
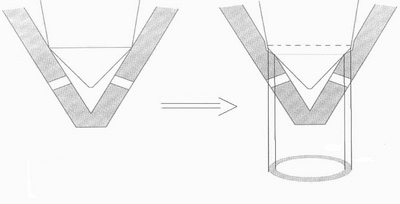
Les aiguilles ont donc été modifiées et sont réalisées avec un second cône de fermeture fiabilise l'étanchéité de l'injecteur et se présentent sous la forme :
Evolution de la commande de l'injecteur électromagnétique Bosch
Avec les constantes évolutions des systèmes d'injection et l'augmentation des pressions d'injection, Bosch a conçu un nouvel injecteur électromagnétique. Celui-ci, moins coûteux qu'un injecteur piézo-électrique, permet de réduire le temps de réaction de commande par rapport à un injecteur électromagnétique conventionnel.
D'aspect tout à fait traditionnel comme le montre la photo ci-dessous, il se différencie d'un injecteur classique par sa commande qui requiert un changement de polarité pour sa fermeture et une tension d'alimentation de 50V au lieu de 80V.
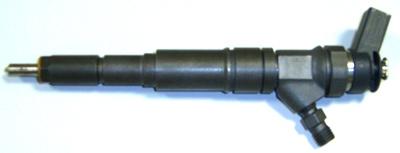
Signal de commande, (oscillo aux bornes de l'injecteur).
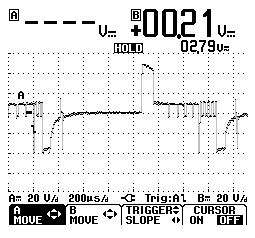
Constatation :
Lors du démontage du porte injecteur, j'ai pu noter une modification de l'électroaimant qui voit sa ferrite magnétisée, une butée mécanique pour l'ancre a été rajoutée et une simplification de l'ancre qui n'est plus composée que d'une seule pièce.
Représentation schématique du porte-injecteur

Les jeux de fonctionnement
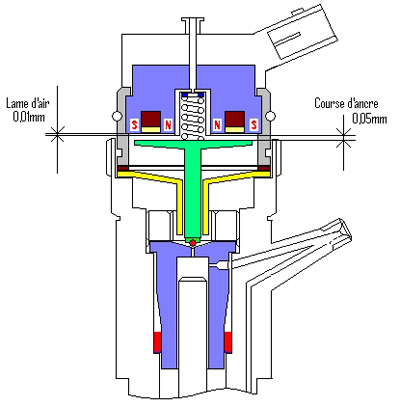
L'insertion d'une butée mécanique d'ancre dans l'électrovanne simplifie le montage par la suppression d'une cale de réglage. La ferrite ayant une très grande perméabilité magnétique mais une très faible résistance mécanique, il faut donc veiller à ce que l'ancre ne touche jamais la ferrite ; un jeu d'1/100 de mm est généralement retenu. Il ne reste plus qu'une cale de réglage pour le réglage de la course d'ancre d'environ 5/100 mm.
Ce type de montage permet une réduction non négligeable de la masse des pièces en mouvement ce qui entraine une plus grande vitesse de déplacement d'ancre.
Fonctionnement
Au repos, la magnétisation de la ferrite ne permet pas d'attirer l'ancre car le ressort est suffisamment fort pour le maintient en position fermée.
Lors de la commande de l'injecteur, le courant circulant dans la bobine crée un champ magnétique qui vient s'ajouter à l'aimantation de la ferrite ; ces deux champs attirent rapidement l'ancre jusque sur sa butée mécanique, l'injecteur est en phase d'injection.
Commande de l'injecteur
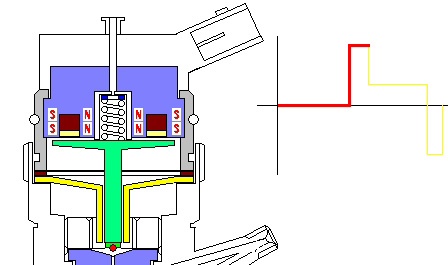
Lors de la fermeture de l'injecteur, il faut donc inverser les polarités d'alimentation de l'électrovanne, durant un temps fixe suffisamment long, afin de créer un champ magnétique permettant d'annuler le champ de la ferrite et permettre au ressort de repousser l'ancre sur la bille, comme le montre la vue ci-dessous.
Fermeture de l'injecteur
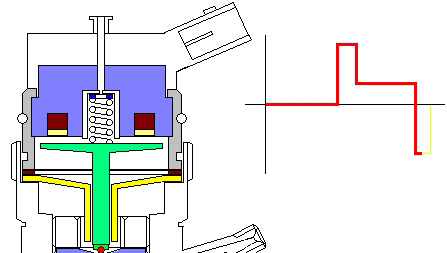
Au terme de ce temps de fermeture, le courant de fermeture est supprimé et le porte injecteur se trouve prêt à être de nouveau commandé.
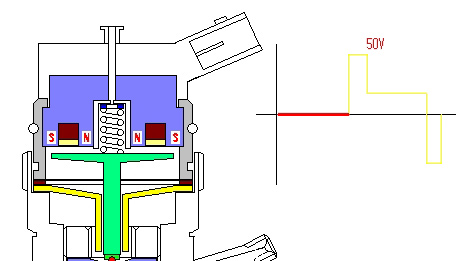
Alimentation électrique
La commande électrique de ce porte injecteur nécessite un étage de sortie, calculateur, en H afin de permettre l'inversion de sa commande.
Schématisation de la commande injecteur (circuit en H)
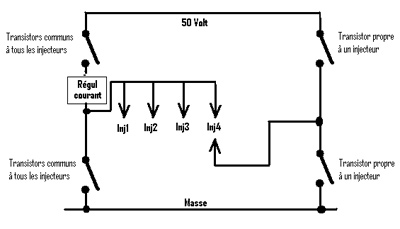
On remarque que les quatre injecteurs sont alimentés en commun sur l'une de leurs bornes et individuellement sur l'autre, ce qui permet l'inversion de leurs polarités.
Evolution de l'injecteur :
A sa sortie, l'injecteur électromagnétique correspond tout à fait aux besoins de la norme Euro 3. Rapidement et en particulier depuis Euro 5, cet injecteur montre ses limites en terme de temps de réponse et de pression maxi. Avec l'évolution des normes et le besoins de découper de plus en plus l'injection (injection multiples lors d'un même cycle moteur) la nécessité de réaliser des post injections avec l'arrivée massive du filtre à particules. L'injecteur Bosch électromagnétique à donc évolué en remplaçant le système de bille par un clapet.
Les équipementiers travaillent sur le caractéristiques suivantes pour l'évolution de leurs injecteurs:
- Pressions d'injection maximales
- Temps de commutation
- Débits de fuite
Description de l'injecteur CRI2.16:
Le CRI 2.16 comporte un élément de commande à bille. Une augmentation de la pression d'injection maximale aurait pour conséquence une réduction de la dynamique de l'injecteur et, par suite, des temps de commutation très longs. La haute pression se trouve au-dessus et en dessous de l'aiguille d'injecteur. L'aiguille d'injecteur est entourée de carburant basse pression. Un inconvénient dû à la différence de pression est le débit de fuite. Par construction, le CRI 2.16 a par conséquent les points de fuite suivants :
- Fuite lors de l'ouverture de l'élément de commande à bille
- Fuite permanente au-dessus de l'aiguille d'injecteur
- Fuite permanente en dessous de l'aiguille d'injecteur.
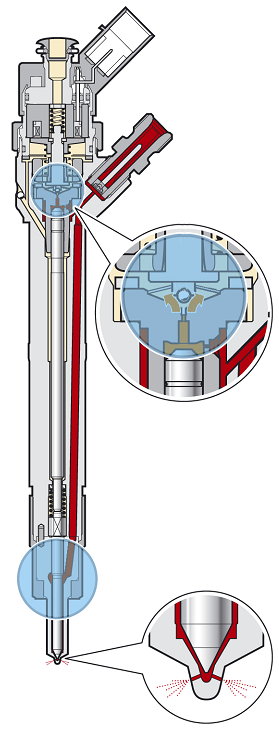
Description de l'injecteur CRI2.18:
Le CRI 2.18 comporte un élément de commande perfectionné. Grâce à l'utilisation d'un élément de commande équilibré en pression, la pression d'injection maximale a pu être augmentée jusqu'à 1800 bar tout en augmentant en même temps la dynamique et en réduisant les temps de commutation. La pression d'injection maximale n'est cependant pas limitée par l'élément de
commande de l'injecteur à électrovanne, mais par les points de fuite dus à la construction. Par construction, le CRI 2.18 a les points de fuite suivants :
- Fuite lors de l'ouverture de l'élément de commande équilibré en pression
- Fuite permanente au-dessus de l'aiguille d'injecteur
- Fuite permanente en dessous de l'aiguille d'injecteur.
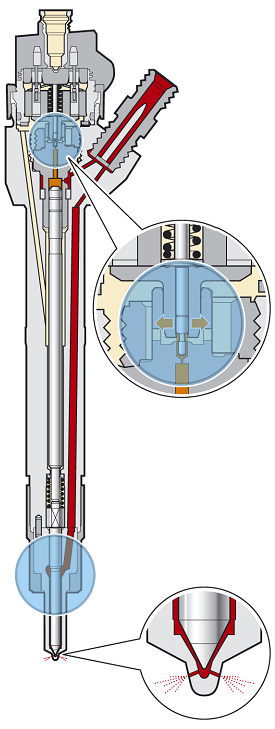
Description de l'injecteur CRI2.20:
Le nouvel injecteur à électrovanne CRI 2.20 est un développement du CRI 2.18. Le bénéfice est une réduction de la consommation de carburant ainsi que
des rejets polluants.
L'injecteur à électrovanne a subi de nombreuses modifications de construction.
Un point commun entre les deux injecteurs est l'élément de commande équilibré en pression. Pour augmenter les pressions d'injection maximales, le débit de fuite a du être réduit. En comparant les injecteurs, on voit que dans le cas du CRI 2.20, l'ensemble de l'aiguille d'injecteur est entouré de haute pression de carburant. Aucune fuite n'a lieu au-dessus et en dessous de l'aiguille d'injecteur. Par construction, le CRI 2.20 uniquement le point de fuite suivant :
- Fuite lors de l'ouverture de l'élément de commande équilibré en pression.
Le nouvel injecteur à électrovanne CRI 2.20 offre en résumé les avantages suivants :
- Pressions d'injection maximales élevées
- Dynamique élevée et, par suite, temps de commutation réduits (7 phases d'injection par cycle de travail)
- Débit de fuite réduit et, par conséquent, pertes de puissance réduites
- Guidage d'aiguille proche de la buse et, par conséquent, très haute qualité de pulvérisation
- Mini rampe et, par conséquent, influence réduite des ondes de pression sur la pression de rampe.
Amélioration de la pulvérisation:
En plus de l'augmentation de la pression d'injection maximale, la qualité de la pulvérisation a été améliorée. Elle a été obtenue grâce à l'introduction d'un guidage d'aiguille à proximité de la buse.
Cela entraîne une réduction des émissions d'hydrocarbure (HC) et de monoxyde de carbone (CO) ainsi qu'une réduction de la consommation de carburant.
Rôle de la mini rampe:
Grâce au volume supplémentaire qui se trouve dans l'injecteur, la mini rampe entraîne une diminution de l'influence des ondes de pression sur la pression de rampe. Cela profite à un dosage plus précis du débit d'injection lors des différentes injections isolées.

Lors de l'ouverture de l'aiguille d'injecteur, des variations de pression surviennent normalement dans la rampe suite au prélèvement. Le volume injecté dépend de la durée d'activation ainsi que de la pression de rampe régnant au niveau de l'injecteur. L'injection du carburant terminée génère une onde de pression qui influence l'injection du carburant suivante avec le même injecteur (injection multiple).
Cet effet a été compensé sur les injecteurs utilisés jusqu'à présent par un modèle de calcul coûteux.
La mini rampe introduite dans le CRI 2.20 permet d'amortir notablement les ondes de pression et entraîne ainsi une réduction des coûts d'application.
Diffusion sur le marché | Les injecteurs à technologie électromagnétique sont utilisés sur environ 80% des moteurs équipés de systèmes Common rail. Les injecteurs piézo-électriques (plus coûteux) équipent le reste des motorisations. |
---|---|
Constructeurs concernés | Tous les constructeurs de moteurs diesel à injection Common rail. |
Innovation engendrant des entretiens | Non |
Innovation engendrant des réparations | Oui |
Types de réparations |
|
Dispositif législatif en rapport avec l'innovation | Depuis la mise en application de la norme de dépollution EURO III (01/01/2000). |
Contrôle technique | L'injecteur lui-même n'est pas susceptible de générer la saisie d'une défaillance, hormis son évidente implication dans une pollution excessive ou une fuite de carburant. |
Mots-clés | Injecteur Common rail, injecteur électromagnétique, Injecteur Bosch, Injecteur à bobine. |
Méthodes et pratiques
Contrôler la résistance des injecteurs avec un multimètre et sa commande électrique avec un oscilloscope.
Contrôler le débit de retour des injecteurs avec des éprouvettes graduées pour mesurer le taux d'étanchéité hydraulique.
Effectuer le remplacement des injecteurs.
Coder les injecteurs si nécessaire avec une valise de diagnostic.
Réparer les injecteurs en remplaçant les éléments internes défaillants.
Le remplacement des injecteurs s'effectue dans les ateliers de réparation automobile, en respectant les conditions d'hygiène et de sécurité préconisées.
Pour la dépose des injecteurs, des arraches à inertie peuvent être utilisées, lorsque la dépose est rendue difficile par l'accumulation de suies au niveau de la buse de l'injecteur. L'utilisation de ce type d'outillage applique une contrainte importante sur l'injecteur. Ses caractéristique de débit, pourrait être modifiées suite à son extraction. Il est donc conseillé de procéder à son passage au banc après cette intervention (la dépose "moteur chaud" si cela est possible est conseillée).
Des outils d'extraction hydraulique existe, ils permettent de retirer l'injecteur de la culasse, lorsque l'arrache à inertie n'a pas été suffisant. L'utilisation de tels outil nécessite le démontage de la bobine de l'injecteur et donc son passage au banc ou son remplacement sera nécessaire.
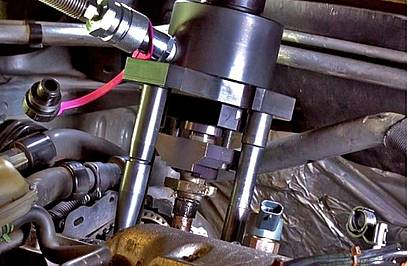
Chaque injecteur neuf, avant de le reposer sur la culasse, doit être muni d'une rondelle pare-feu neuve. Le logement dans la culasse doit être parfaitement propre pour recevoir l'injecteur neuf. Pour cela il existe un kit de nettoyage.
Contrôle et diagnostic:
Sur un injecteur électromagnétique, il est possible de contrôler l'électroaimant en mesurant sa résistance et son isolement.
Exemple R=0,4±0,1?
Il est possible, à l'aide d'un oscilloscope et d'une pince ampèremétrique (petit calibre) de mesurer la commande en tension et en intensité sur chaque injecteur (voir exemple).
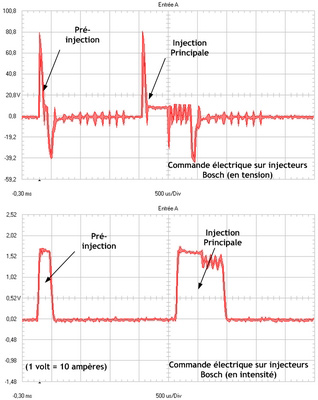
Classification des injecteurs :
Afin de palier les dispersions de fabrication et d'usinage, certains injecteurs sont identifiés par la classe et d'autres par le codage.
Injecteur classé :
Les classes sont :
1/2/3 (chiffre numérique)
X/Y/Z (caractère alphabétique)
Bleu/jaune/rouge (couleur)
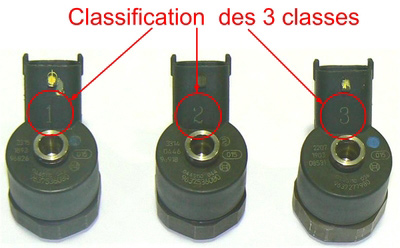
Les injecteurs portant un code : code IMA (Injektor Mengen Abgleich)
Ce code doit être entré dans le calculateur avec une valise de diagnostic ; il correspond à la caractéristique électro-hydraulique de l'injecteur. Cela permet au calculateur de connaître la position sur le moteur de chaque injecteur et de doser plus précisément le carburant injecté dans chaque cylindre.
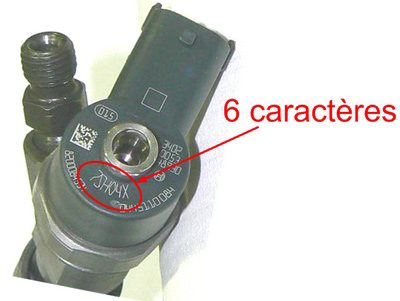
Pour répondre aux normes de dépollution et sans cesse améliorer l'agrément de conduite, le calculateur corrige les débits injectés sur chaque cylindre. C'est-à-dire qu'il analyse le couple fourni par chaque cylindre via le capteur régime et qu'il égalise ces rendements en faisant légèrement varier les débits. C'est-à-dire que chaque injecteur d'un même moteur est commandé avec un temps différent. Cette correction n'est valable que jusqu'à un certain régime.
Ces corrections sont exprimées en mm3/coup ou en mg/coup.
La réparation des injecteurs est possible en atelier spécialisé qui sont équipés du matériel nécessaire à la réfection de ces injecteurs. A ce jour toutes les pièces sont référencées et disponibles pour la réfection des injecteurs Bosch électromagnétiques. Le prix est environ divisé par quatre par rapport à un injecteur neuf.
Sur ces injecteurs, il est possible de contrôler le débit de retour hydraulique des injecteurs, en utilisant des éprouvettes. Cela permet de connaitre le niveau d'étanchéité de chaque injecteur. Ce contrôle est à effectuer lorsque le système de gestion moteur détecte des chutes de pression dans la rampe.
Exemple pour des injecteurs Bosch sur un moteur chaud tournant au ralenti :
Débit de retour maxi sous 3 min : 22 ml
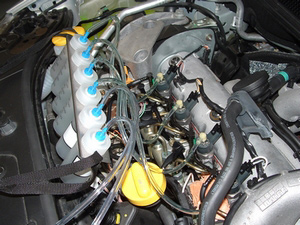
Dans le cas d'un véhicule qui ne démarre pas à cause d'une pression de rampe trop faible, il faut effectuer une mesure des débits de retour à l'aide de tuyaux transparents. C'est-à-dire qu'il faut mesurer, sous action démarreur, la longueur de gasoil dans les tuyaux. Il n'existe pas de valeurs de référence, mais la comparaison entre les 4 injecteurs permet d'effectuer un diagnostic.
Entreprises concernées aujourd'hui | Véhicules industriels, Spécialistes, MRA, RA2, RA1 |
---|---|
Métiers concernés | Encadrement d'atelier, Mécanicien technicien VI-VU, Mécanicien-Technicien Auto |
Précisions sur les métiers concernés | Pour les MRA, RA1, RA2, les spécialistes et les véhicules industriels : activité de diagnostic, de contrôle et de remplacement des injecteurs électromagnétiques. Cependant, le codage des injecteurs n'est possible qu'avec une valise de diagnostic. |
Impact sur les compétences en atelier
- Savoir lire un schéma électrique et la documentation technique.
- Connaître le fonctionnement d'un système common rail.
- Savoir utiliser une valise de diagnostic et d'interpréter ses données.
- Savoir effectuer des contrôles électriques avec un multimètre et un oscilloscope.
- Savoir appliquer une méthode de dépose repose d'un injecteur.
- Pour les spécialistes (diésélistes) il faut en plus, être en mesure de réparer les Injecteurs électromagnétiques et d'effectuer leurs contrôles sur des bancs spécifiques.
Exemple d’outillage approprié
- Valise de diagnostic,
- Documentation technique,
- Multimètre,
- Oscilloscope
- Eprouvettes graduées.
- Pour les spécialistes, banc de contrôle des injecteurs, et appareil de démontage spécifique.
Exemple de banc de contrôle des injecteurs:
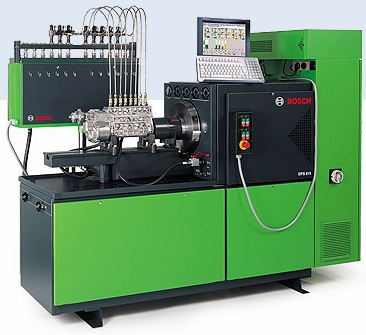
Source Bosch
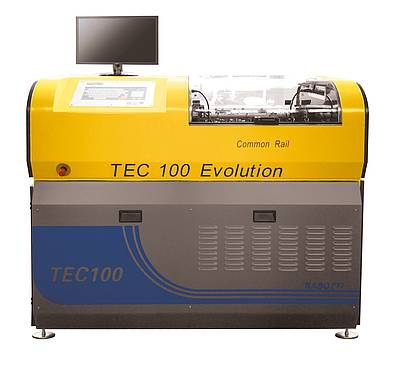
Source Rabotti
À lire aussi dans la même section

Les pompes haute pression
Les pompes hautes pression sont au coeur du système d'injection. Elles permettent la création de la haute pression et alimentent les injecteur en gazole. Les pompes hautes pression peuvent être...

Les circuits d'alimentation basse pression diesel
Le circuit d'alimentation est méconnu du grand public mais pas entièrement. En effet, il est très courant d'entendre parler de remplacement de filtre à gazole.
Bon nombre de gens ont, malheureusement...
Les biocarburants diesel
Le biocarburant contient une part de carburant produit à partir de matériaux organiques non issue du pétrole.
La Dénomination du carburant gazole vient d'évoluer, vers le nom B7 en Europe, cela...
La régulation électronique des pompes distributrices VP Bosch
Le système de pompe rotative à régulation électronique à été développé par Bosch. Monté depuis 1987 chez BMW cette innovation à permis plus de souplesse moteur, de meilleures performances ainsi qu'une...